From Spaghetti to Success: A Time and Motion Study Case Study
- Peter Assad
- Jan 23
- 2 min read

Introduction
Inefficient layouts and excessive motion waste can significantly hinder a business’s productivity. In this case study, we’ll showcase how Elora Consulting helped a client transform their operations using a Time and Motion Study. From a disorganized "Spaghetti Diagram" to an optimized, lean layout, the results were transformative.

The Challenge: Excessive Motion Waste
Our client’s facility suffered from a poorly designed layout that caused employees to take unnecessarily long paths to complete tasks. This not only wasted time but also impacted employee satisfaction and increased operational costs.

What is a Spaghetti Diagram?
In Lean and Six Sigma, a Spaghetti Diagram is a visual representation of the flow of activities, movements, or materials within a process. It highlights inefficiencies by mapping out the paths employees or resources take to complete tasks. The diagram resembles a tangled mess of spaghetti, emphasizing excessive motion, backtracking, and unnecessary travel distances.

Why Use a Spaghetti Diagram?
Identify Motion Waste: It reveals areas where excessive movement occurs, which can lead to wasted time and effort.
Enhance Layout Design: By visualizing inefficiencies, it provides insights for optimizing operational layouts.
Improve Productivity: Reducing unnecessary motion results in faster and more efficient workflows.
Spaghetti Diagrams are a foundational tool in Lean and Six Sigma, providing a clear picture of where improvements are needed to streamline processes and eliminate waste.

The Solution: Applying the Time and Motion Study
Step 1: Data Collection: We observed workflows and created a "Spaghetti Diagram" to visualize motion waste.
Step 2: Analysis: The diagram highlighted excessive back-and-forth movement between workstations.
Step 3: Redesign: Collaborating with architects, we proposed a new layout that reduced motion waste and improved task flow.
Step 4: Implementation: The updated layout was implemented with minimal disruption to operations.

The Results: Before and After
Before: Employees walked an average of 3 miles per shift due to inefficient layouts.

After: Optimized workflows reduced average walking distance by 60%, saving over 1,200 hours annually.

Additional Benefits: Cost savings, increased productivity, and improved employee satisfaction.
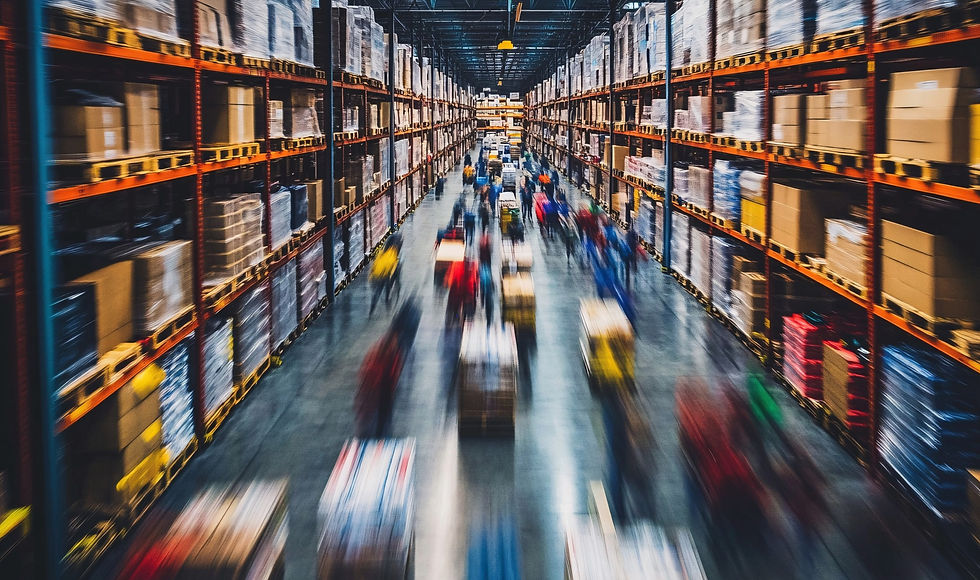
Conclusion
This case study demonstrates the tangible impact of a Time and Motion Study. By reducing motion waste and optimizing layouts, businesses can achieve remarkable results. Contact Elora Consulting to learn how we can help transform your operations and boost efficiency.